واسبراتير عادى مش الكترونى
وموبينه الكترونى!!!!!!!!!!??????? ?
this is not good
it will
destroy and damage your contact points
nearly soon then so take a good care as well about that
!!!!!!!!!!!!
is that yours
???????/
45000 volt
60000 Volt
16.000 volt
or
this one
????
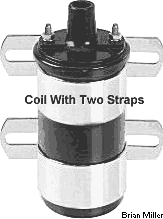
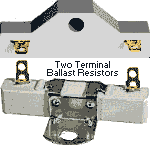
Some ignition coils require an external ballast resistor (off any 1955-57 General Motors vehicle) or a full-length resistance ignition wire (off any 1958-74 GM vehicle) to prevent from putting too much voltage through the primary circuit and ignition points, which could burn them up. A ballast resistor or resistance wire is basically a voltage reducer that reduces 12 volts down to anywhere between 6-9 volts, depending on the load. (The ballast resistor shown here is the same used on the 1955-57 GM vehicles.) But if a coil reads "12 VOLTS" on its casing, then it has a built-in resistor. A resistor may not be needed with many new coils because most of them nowadays have a built-in resistor. And using a resistor doesn't effect the voltage output of a coil. It only prevents from burning it up, and it saves wear on the ignition points. The reason manufacturers don't install a resistor inside some high-performance coils is because these coils draw more amps from the battery. This causes the resistor to operate at a higher temperature, which could overheat and damage the windings within the coil. If you prefer to use a high-performance coil, when you purchase one, be sure to ask the salesperson if it has a built-in resistor or if it requires an external one. This is important for the life of the coil.
When testing a ballast resistor for voltage drop, it won't show any resistance unless there's a functioning load on it with electrical current going through it, such as the ignition coil and/or control module with the engine running. With battery ignition, most high-performance ignition coils requires two condensers [connected to the ignition points] for quicker saturation at higher rpms but the points won't last as long because of the increased amperage that the coil draws. And a high-performance coil has no effect whatsoever with crank trigger ignition when using a Chrysler or Ford ignition control module. And most stock coils produce more than enough voltage for even the hottest high-performance engines built, especially when used with the crank trigger ignition.
The way we test a stock coil is we connect it in a circuit, like it's on an engine and if it produces a spark with at least a 3/4" wide gap, it's a good coil. A high performance coil should produce a spark with a wider gap.
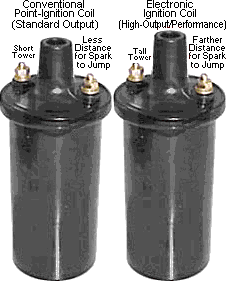
All conventional point-type ignition systems that's installed on garden tractor and automotive engines utilizes a standard output [20,000-30,000 volt] coil. And all automotive electronic ignition systems utilize a high output [40,000-60,000 volt] coil. The differences in these coils is by the height of the center tower. The high output coil has a taller tower, to keep the spark from shorting to the terminals. So if you want more spark, instead of using a high dollar, aftermarket high-performance coil, you could just use a low-cost automotive one that's designed for an automobile with electronic ignition. (Early Chrysler and Ford products.) On any ignition system, the voltage of the coil is the same at any rpm. The only way a coil will produce more voltage is when the spark plug gets weak or the gap on the spark plug is widened. The coil will produce less pulses of voltage at idle speeds and more pulses at higher rpms. But the amount of voltage will stay the same.
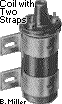
If you've ever experienced the metal strap on your ignition coil of breaking due to normal engine vibration (especially at high rpms or wide open throttle) and because the metal itself is too thin, then what you need to do is either fabricate a strap made of thicker metal, or install two coil straps as shown in the picture to the right, and be sure to fasten the straps securely. This will double the life of the clamps and lessen the chances of either strap of ever breaking again. Ever had a good run going down the track and all of a sudden your engine dies, and then you found it was because of a faulty ignition coil? Well, chances are it wasn't designed for use on a garden pulling tractor. Even new coils have been known to fail in a very short time on a garden pulling tractor. The reason some coils fail is due to single cylinder engine vibration running at high rpms or wide open throttle. The tiny wires (or windings) inside an oil filled coil will vibrate and break over time. Even the insulation on the windings themselves will "rub" or scrape against the other internal wires, resulting in a short, and coil failure. That's why it's best to use an
epoxy-filled coil to prevent the windings from vibrating, shorting out and/or breaking. The epoxy holds the wires solid, resulting in no vibration of the windings whatsoever. So for the little difference in price, accept no substitutes! Epoxy-filled coils are most reliable for use on a garden pulling tractor. Part numbers for epoxy-filled coils are: Borg Warner # BWD E81 (with an internal resistor); OEM Kohler coil # 231281; NAPA # 7-01643; Borg Warner # BWD E40P (requires an external resistor).
JEG'S (
http://www.jegs.com),
Summit Racing (
http://www.summitracing.com),
J.C. Whitney, Inc. (
What Cause Some Ignition Coils To Go Bad?
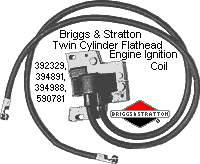
On the Briggs & Stratton twin cylinder flathead engine, after several years of use, the ignition coil (rather with points or Magnetron) will fail to produce a spark. This happens often on these engines because one coil must fire two spark plugs with a gaps set at .030" each. This is the same as firing one spark plug with a .060" gap. Most magneto coils are not designed to produce this much voltage. The coil is forced to produce the voltage to fire both plugs and this causes it to overheat, and eventually burn up. To lessen the chance of the coil going bad (again), set the plug gaps at .015" each. This will simulate having just one spark plug with a gap of .030", and the coil will operate cooler and last longer. The engine will run the same, with no loss of power.
Or instead of doing the above, if an older Briggs & Stratton twin cylinder flathead engine has points, it can be easily converted to the more reliable battery ignition (for a hotter spark and more power). The B&S ignition points can be still used, but two automotive canister-type ignition coils (with spark plug wires), and two battery ignition condensers will have to be used. The spark plug gaps will need to be set at .035", and the ignition timing can be set by the gap of the points (.020") or with an inductive timing light after the flywheel is degreed in with timing marks. And for anyone who's wondering, an ordinary automotive battery-type condenser with an automotive canister-type ignition coil will work on any one or two cylinder air-cooled engine that use the battery ignition system. But when using two automotive ignition coils on a twin or two cylinder engine with conventional points, be sure to use two condensers as well, one for each coil , only if the coil(s) requires one. Otherwise, the engine will idle, but won't rev up much. And there's a very little difference between the Kohler battery-type condenser and an automotive [Chevrolet/GM] condenser. So either can be used on a small engine.
now mar egypt
what do you think about your ignition coil???????/!!!!!!
fo new models

?????????????????????????/!!!!!!!!!!!!!!!!!!!
